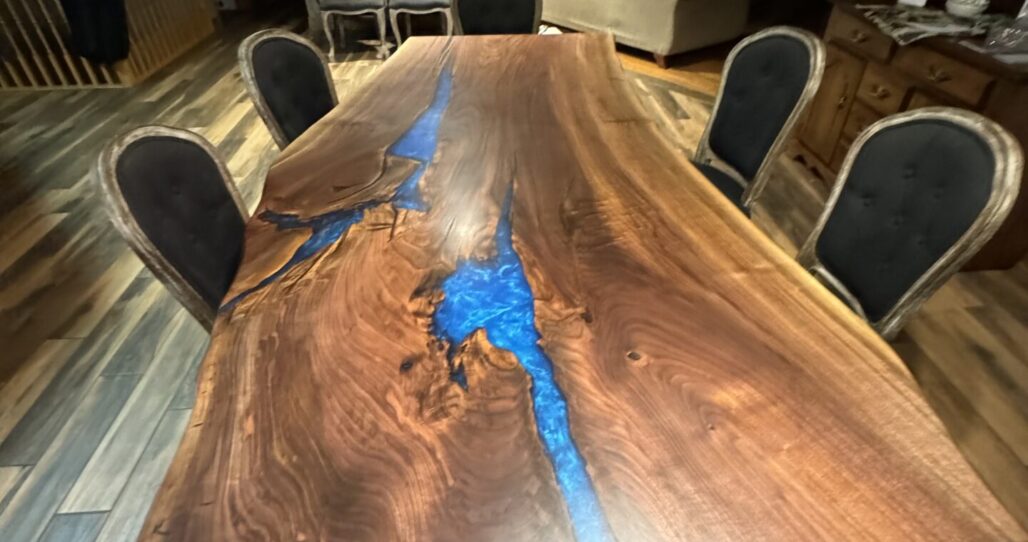
Essential Tips and Tricks for Making Epoxy Tables: A Guide for Beginners and Pros Alike
Epoxy tables have become a popular trend in woodworking, with their beautiful, glass-like finish and unique, custom designs. Whether you’re just starting out or already have experience in woodworking, there are some key tips and rules to follow when making epoxy tables to ensure you get the best results. In this blog post, we’ll cover the most important rules and techniques to help you succeed with epoxy table making.
- Don’t Be Afraid to Share Your Knowledge
When I first started sharing tips and techniques for making epoxy tables, many people questioned why I was giving away “secrets” that could help my competitors. At the time, I didn’t have a clear answer. But looking back, I realize that sharing my knowledge has brought me more success than I ever anticipated. Today, my business has evolved from a small, part-time woodworking shop into a thriving lumber mill and furniture manufacturer that generates enough income for me to be able to do this full time and support my family.
The point here is: don’t be afraid to share your knowledge. If you help others, you might be surprised by how much you’ll get in return.
- Limit Your Epoxy Pours to Avoid Issues
One of the most common mistakes people make when pouring epoxy is going too thick. While some manufacturers might claim you can pour up to four inches of epoxy in a single layer, I highly recommend sticking to a maximum of 2.5 inches. In my experience, pouring too thick of a layer can lead to overheating, cracking, and other issues that are difficult (or even impossible) to recover from.
For beginners or those who are uncertain, I suggest limiting pours to 2 inches. If you have a table that’s 3 inches thick, consider doing two separate pours: one for the base and a second to top it off. This will minimize the risk of a disastrous reaction like overheating, cracking, or smoking, which could completely ruin your project.
- Work with Dry Wood
It might sound obvious, but it’s crucial to use dry wood for your epoxy table projects. Green or wet wood can cause complications when combined with epoxy, leading to warping, cracks, or other undesirable results. Before working with any wood, make sure to use a moisture meter to ensure that the wood is properly dried. If you’re buying wood from a supplier, it’s always a good idea to ask for confirmation that the wood has been dried to a safe moisture level. Always purchase live edge wood slabs from a reputable supplier.
Also, ensure the wood is treated for pests, either through kiln drying or with chemicals, to avoid any infestation issues in the future.
- Choose High-Quality Epoxy
The quality of the epoxy you use is critical for the success of your project. While you don’t have to use the exact brand I personally prefer, always invest in high-quality, premium epoxy. Not all epoxy resins are created equal, and using cheaper or lower-quality options can result in poor finishes, cracking, or yellowing over time.
Once you’ve chosen your epoxy, it’s crucial to mix it thoroughly. Don’t just follow the time instructions on the label; focus on how well you’re mixing the epoxy. For example, if you’re using a paddle mixer, ensure you mix evenly along the sides, bottom, and top to avoid unmixed epoxy. Some people make the mistake of mixing for the full recommended time without focusing on the thoroughness of the mix, which can lead to inconsistencies in the final product.
- Avoid Scraping the Sides of the Bucket
When pouring epoxy, be cautious not to scrape the sides of the bucket. While it might seem tempting to scrape every last bit out, this can result in unmixed material being transferred into your project, affecting the final outcome. Instead, let the epoxy pour out naturally, without scraping the sides. This will help avoid contaminating your mixture and ensure a consistent, smooth finish.
- Seal the Top of Your Wood Slabs
One of the most important yet often overlooked rules when making epoxy tables is to seal the top of your wood slabs. When you’re working on a river table or similar project, the bottom of the wood slab will be sealed by the epoxy you pour. However, the top of the wood is exposed to air, which can cause moisture to seep into the wood over time. This can lead to warping, cracking, and twisting, ultimately ruining your project.
To prevent this, always seal the top of your slabs with a layer of shellac, epoxy, or polyurethane before you begin pouring your epoxy river. This protective layer will ensure that moisture from the air doesn’t affect the wood, preserving the quality of your work.
- Consistency and Patience are Key
Like any woodworking project, epoxy table making requires patience. Rushing through any part of the process can lead to mistakes, and this is especially true when working with materials like epoxy. Take your time to prepare your wood, mix your epoxy, and ensure the conditions are ideal for a successful pour.
Remember, it’s better to do things slowly and correctly than to rush and risk ruining your project.
Conclusion: Get Started on Your Epoxy Table Project with Confidence
Epoxy table making is a rewarding craft, but it’s important to follow the right rules and techniques to ensure a beautiful, lasting product. Whether you’re a beginner or a seasoned woodworker, these tips should give you a solid foundation for your next project.
By sharing your knowledge, using high-quality materials, and following best practices, you can elevate your woodworking skills and create stunning epoxy tables that will impress your clients—or your friends and family. So, if you’ve enjoyed these tips, don’t forget to contact us for your next live edge wood project to take your woodworking to the next level.
lets talk live edge wood slabs
Feel free to call or text Mike at (416) 618-0081